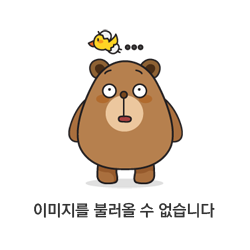
사출 공정에서 가장 중요한 도구인 사출 금형에 대해 알아봅시다
사출 금형이란?
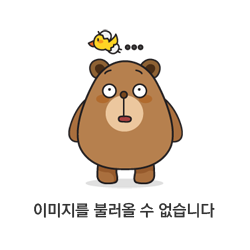
금형은 제조 분야에서 제품을 생산하는데 사용되는 도구로 재료의 소성, 전연성, 유동성 등의 성질을 이용하여 사출, 프레스 등의 제조 과정을 통해 원하는 제품을 만드는 툴입니다. 내구성 강한 금속 재료를 사용하여 만들어진 틀(형)로, 동일 규격의 제품을 대량으로 생산하기 위한 도구이죠.
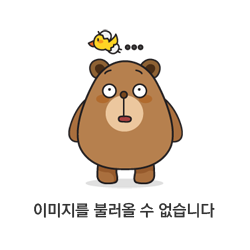
사출 금형은 사출 공정에서 사용하는 금형이며, 플라스틱 원료를 사용하여 동일한 형태의 제품을 대량으로 생산하기 위한 도구입니다. 금형을 먼저 닫은 후 플라스틱 재료(수지)를 녹여 액체 형태로 만든 뒤 고온과 고압으로 금형 내에 주입한 뒤 급속하게 냉각시켜 원하는 형태의 플라스틱 제품을 제작하죠. 일상 생활 용품, 의료, 자동차, 반도체, 제조업 등 거의 모든 분야에서 사용하는 플라스틱 제품들이 이 사출 공정과 사출 금형에 의해 만들어집니다.
사출 금형의 종류
사출 금형에는 목적과 용도에 따라 다양한 종류가 있으나 오늘날 사용하는 사출 금형은 크게 2단 금형, 3단 금형 그리고 스택 금형으로 나눌 수 있습니다.
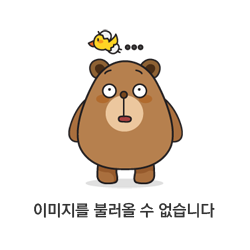
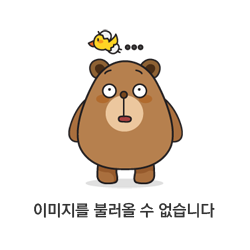
먼저 2단 금형은 가장 기본적인 사출 금형의 구조이며 금형 제작 시 제조 비용이 상대적으로 저렴하며 일반적으로 단순한 형상을 제작 할 때 일반적으로 사용됩니다. 2단 금형은 크게 두 면으로 나눌 수 있는데요, 사출 성형 시 한 면은 고정되어 있고 다른 한 면은 이동하면서 금형을 열고 닫히며 제품을 만들어 냅니다. 냉각 직후 금형을 열면 움직이는 금형 쪽에 플라스틱 러너(찌꺼기)가 붙어있는 성형품이 남게 되는데, 이 러너를 제거해야 비로소 완성품을 얻을 수 있습니다. 이 러너를 제거하는 방법은 성형 후 니퍼 등으로 자르거나 금형 내에 핫런너라는 별도의 장비를 장착하는 것이며 핫런너에 관해서는 따로 포스팅을 하겠습니다.
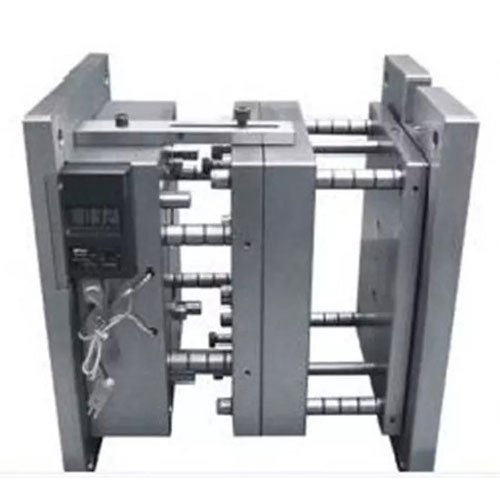
3단 금형은 사출 되는 공간이 두 부분으로 구분됩니다. 가운데의 금형을 두고 한 공간에는 러너가 생산되며 다른 한 공간에서는 제품 본품이 만들어 집니다. 사출 후 금형이 열리는 과정에서 러너가 제품에서 분리되므로 2단 금형과는 다르게 별도로 제거할 필요가 없습니다. 3단 금형은 2단 금형보다는 제작 비용이 비싸지만 핫 러너를 장착하는 것보다 저렴하고 핫 러너 금형보다 파손 가능성이 적습니다. 또한 열에 민감한 재료의 경우 열화 될 가능성이 적습니다. 반대로 단점도 있는데, 성형 사이클 타임이 길고 소모하는 재료 소모가 많으며 더 큰 사출 압력을 필요로 합니다.
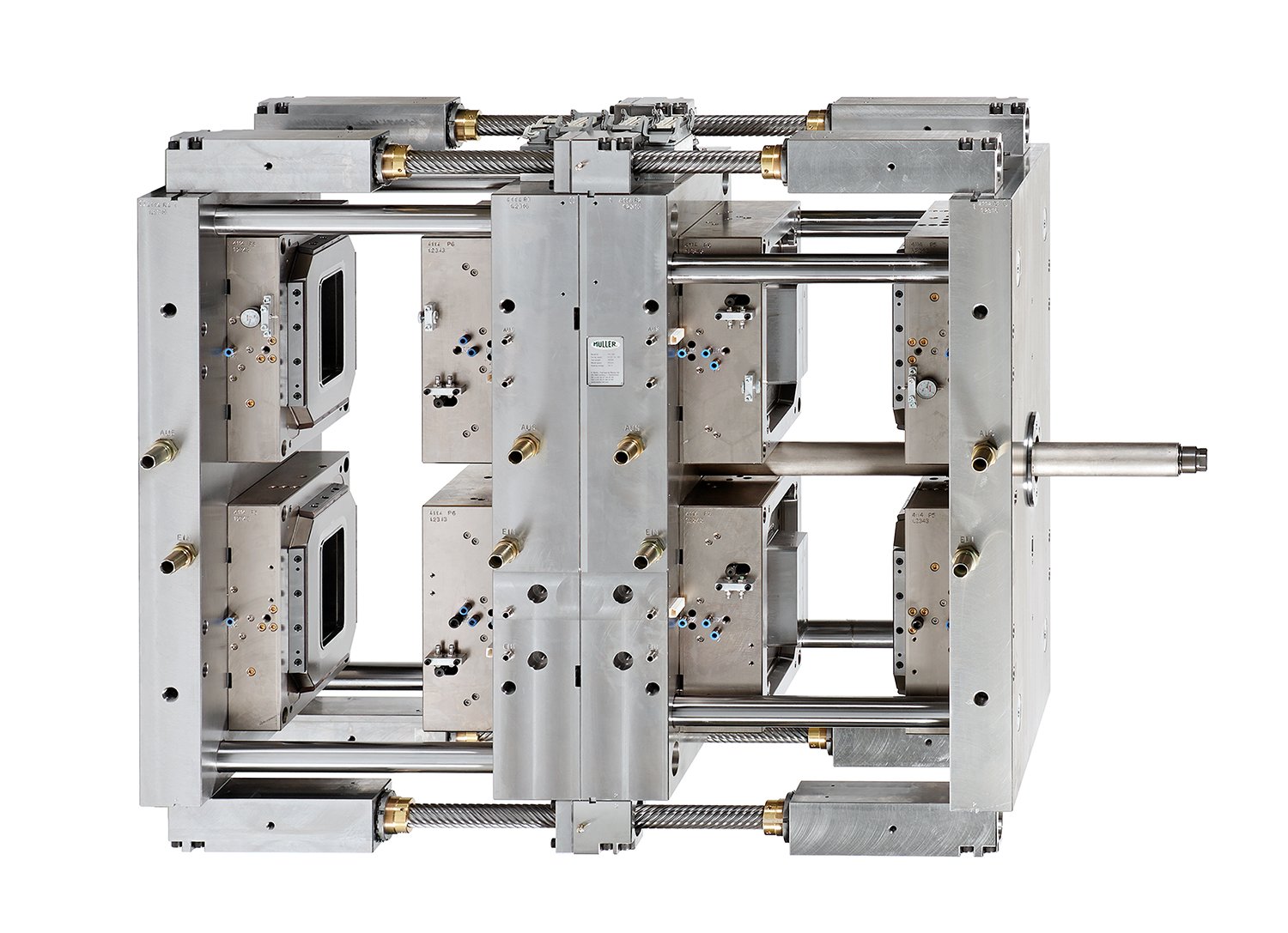
마지막으로 스택 몰드(금형)입니다. 스택 몰드는 금형 양방향에서 제품이 사출하는 금형으로 중첩금형 또는 양면 사출 금형으로 부르기도 합니다. 금형 양쪽에서 성형품을 만들 수 있기 때문에 사출 사이클 시간을 단축시키고 에너지 및 재료 효율이 높아진다는 장점이 있습니다. 사출기 추가 설치나 사출기 갯수를 늘리지 않고도 부품 생산 효율을 높일 수 있는 것이죠. 또한 양쪽에 다른 성형품이 제작될 수 있도록 설계하여 한 번의 사이클로 동시에 두 개 이상의 완성품을 찍어낼 수 있습니다.
스택 몰드 역시도 치명적인 단점 몇 가지가 있습니다. 우선 금형의 설계가 어렵고 제작 기간이 오래걸리며 그만큼 금형 가격도 훨씬 비싸집니다. 다른 금형에 비해 사이즈 또한 크기 때문에 사용 하기 위해서는 상대적으로 더 큰 사출기가 필요하며 스트로크, 최대 사출용량, 스택 몰드의 지지 구조, 사출기의 강성 등 사출 조건 역시도 제한적입니다. 이러한 이유로 스택 몰드의 상용화는 아직까지도 진행중입니다.
2단 금형과 3단 금형의 구조
마지막으로 2단 금형과 3단 금형의 구조, 각 부위의 명칭에 대해 알아보겠습니다.
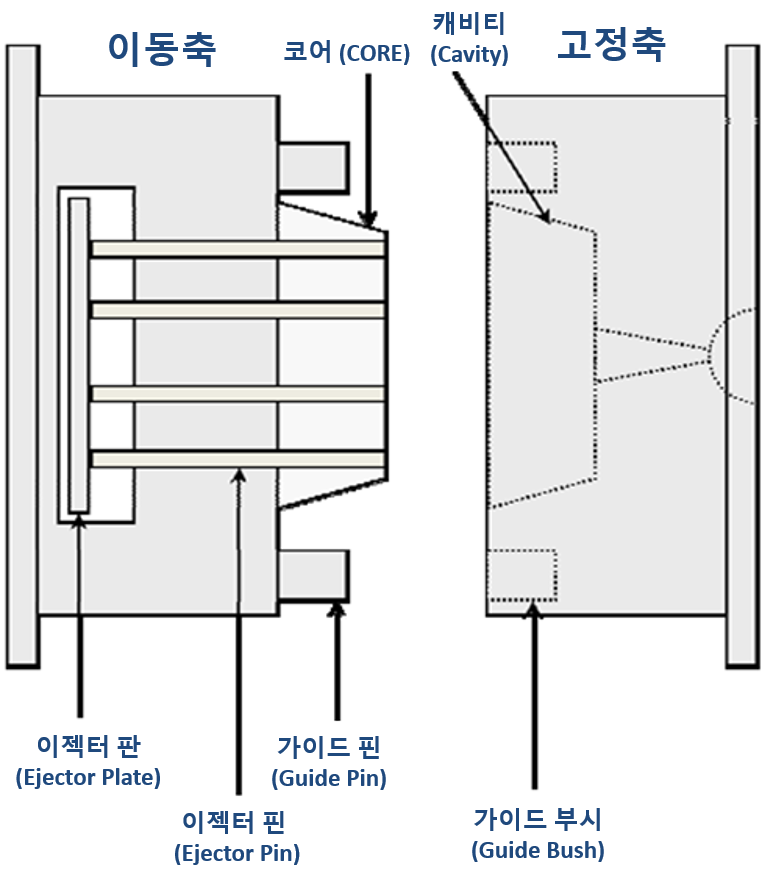
- 몰드 베이스(Mold Base): 캐비티와 코어를 지탱하는 블록
- 코어(Core): 이동측의 성형품면
- 캐비티(Cavity): 고정측의 성형품면, 일반적으로 외관
- 이젝터 핀(Ejector Pin): 완성된 제품을 금형으로부터 취출시킴 (금형에서 제품을 밀어냄)
- 이젝터 판(Ejector Plate): 이젝터 핀을 밀어주는 판. 이젝터 로드에 의해 작동됨
- 가이드 핀(Guide Pin)/가이드 부시(Guide Bush): 금형이 정확하게 닫히도록 하는 역할
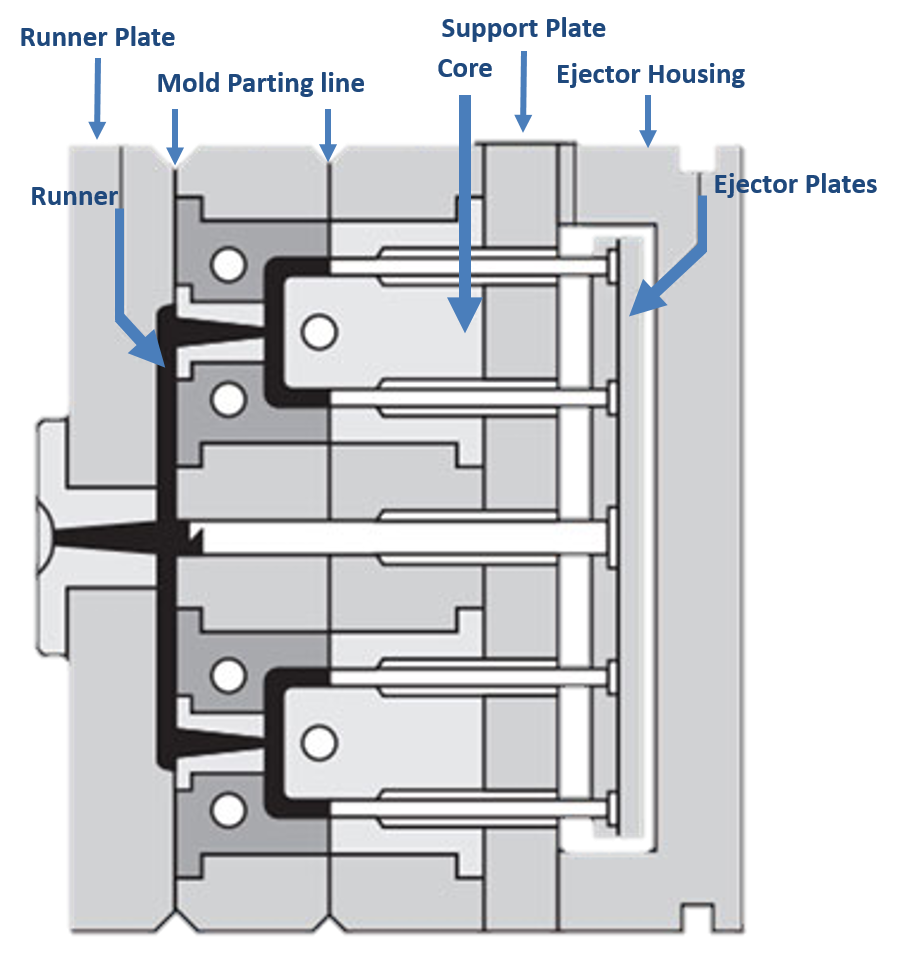
- 런너 플레이트 (Runner plate): 러너(스프루)가 생성되는 공간
- 런너(Runner): 액체 플라스틱이 흐르는 통로, 플라스틱 찌꺼기
- 코어(Core): 성형품 본품이 생성되는 공간
- 이젝터 핀(Ejector Pin): 완성된 제품을 금형으로부터 취출시킴 (금형에서 제품을 밀어냄)
- 이젝터 판(Ejector Plate): 이젝터 핀을 밀어주는 판. 이젝터 로드에 의해 작동됨
'사출 > 사출 이론' 카테고리의 다른 글
핫 런너 시스템(hot runner system)에 대해 알아보기-2 핫 러너 시스템의 종류, 분류 (0) | 2022.02.09 |
---|---|
핫 런너 시스템(hot runner system)에 대해 알아보기-1 핫런너의 뜻과 장단점 (0) | 2022.01.26 |
플라스틱 사출기의 기본 구성 및 사출 성형기의 구조 용어 (0) | 2021.11.09 |
플라스틱과 사출 성형기의 역사, 사출 성형이 오늘날에 이르기까지 (0) | 2021.11.06 |
사출 이란? 사출 성형의 정의와 과정 그리고 사출 구성 요소 (0) | 2021.10.29 |